pioneer machinery
Pioneer smart manufacturing
Pioneer SmartFA platform provides modularized application services such as Smart manufacturing, Smart Analysis and Smart Quality control. In order to eliminate or at least greatly reduce the loss from unexpected down time, Pioneer Machinery in collaboration with worldwide leading bearing manufacturer SKF have developed a vibration analysis technology based on IIoT. This application service module is not only able to monitor and evaluate machine healthy status during production but also to estimate potential risk of failure in future (predictive failure analysis).
Pioneer machinery
Problem faced by the Wire & Cable industry
Cable manufacturers usually adopt a periodic maintenance approach as their main maintenance method. However, due to the high frequency of unexpected failures on some key components, such as bearings, customers are bothered by the correlation between cost and effect of the maintenance frequency.
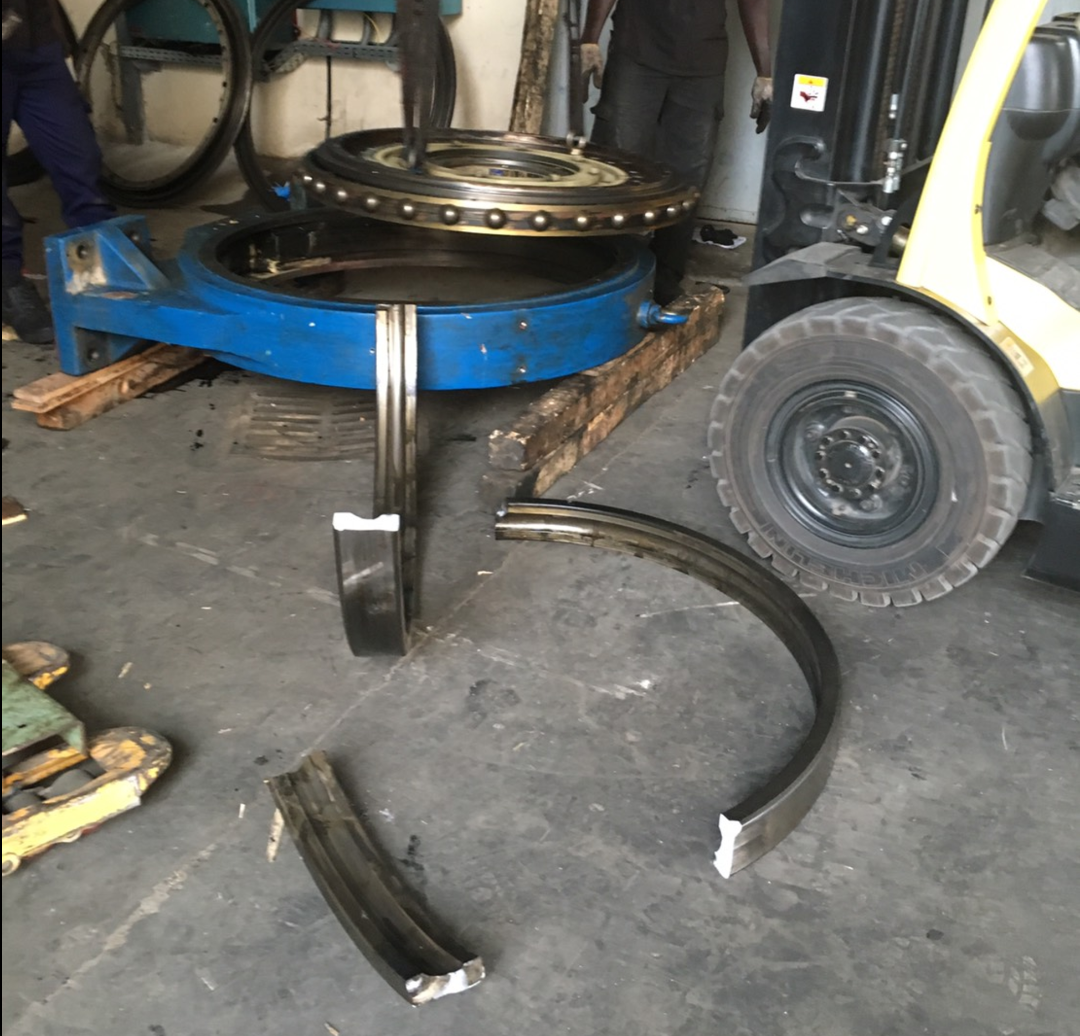
Pioneer machinery
applicable machines
pioneer machinery
Solutions of predictive maintenance
Pioneer machinery
X
SKF
In order to solve the problems of unexpected failure, Pioneer Machinery in cooperation with the top leader bearing manufacturer SKF, introduces a solution based on the analysis of the vibration acceleration at each bearing seat and the performance of an harmonic analysis based on this data. After analyzing data such as dynamic loading, torque on the bearing, deformation and so on, the system is capable of detecting the abnormality and informing ahead of the problem.
Pioneer machinery
Benefits of the predictive maintenance
related applications
CRM form will load here
© 2022 All rights reserved.